3d Printing Phoenix converts computer-aided design (CAD) models into physical three-dimensional objects by adding material one layer at a time. It is a rapidly developing technology and offers many advantages to manufacturing processes.
For example, GE Aviation’s LEAP engine uses 3D-printed Cobalt-Chrome fuel nozzles, which weigh less and are five times stronger than traditional nozzles.
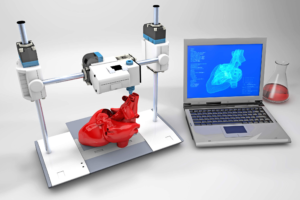
Rapid prototyping is a key component of the design process that allows engineers to move quickly from digital models to physical prototypes. This will enable designers and engineers to create various iterations based on user feedback, ultimately delivering a superior product. This approach to prototyping also helps companies avoid costly revisions during production and save money on manufacturing costs.
The most important thing to remember when creating a prototype is to define its purpose. This will help you prioritize efforts (each prototype is made to achieve a specific goal) and cut costs (you don’t want to spend weeks or months building something that won’t work in the real world). To get the most out of your prototyping, include stakeholders from start to finish. This will ensure that all users understand the feedback you’re getting and provide valuable input.
Prototypes can be low fidelity or high fidelity, depending on the application. High-fidelity models are more accurate representations of the final product and are ideal for user testing. Low-fidelity prototypes, on the other hand, are used for proof of concept and visual communication. They’re often made from less expensive materials and can be produced in a short timeframe.
When choosing a prototyping method, consider how the results will affect user experience and design. For example, if your goal is to test the ergonomics of a new product, you’ll want to choose a method that can produce realistic products with natural feel.
3D printing is an excellent option for producing rapid prototypes. This technology enables the creation of high-quality parts that can withstand a variety of environmental stresses and conditions. It can be used to create engineering prototypes and conduct in-house or field testing for manufacturability. In addition, it can be used to generate detailed, high-performance models that mimic the look and feel of the final product.
In addition, 3D printing is a great way to reduce the amount of raw material used in the production of a product. This can lower the cost of a finished part, especially if it is made from plastic or metal. This technology can also be used to make molds and masters, which are the basis for a finished product.
Additive manufacturing
Additive manufacturing (AM) combines digital design with the construction of three-dimensional objects using a range of processes that build up materials, layer by layer. These include laser sintering, stereolithography and selective laser sintering, among others. The result is a product that has the appearance and properties of a real-world object. Additive manufacturing is an increasingly important technology in a variety of industries, including aerospace, healthcare, consumer products and automotive. Companies can use it to reduce product development times, improve quality and increase flexibility.
Compared to traditional manufacturing methods, additive manufacturing allows designers to change designs without the time and expense associated with tooling changes. It also helps manufacturers avoid costly retooling and reduce the amount of waste material. It can also be used to produce complex parts that would be impossible to make by hand. For example, Phoenix-based company Local Motors printed a prototype of a car at the North American International Auto Show in less than an hour.
The additive manufacturing process also enables companies to create new, innovative products and services. For example, 3D printing enables sports and gear manufacturers to create personalized equipment for athletes. This technology also enables manufacturers to produce parts that are lighter, stronger and more versatile. It can also be used to print medical devices, such as splints and supports, or even replacement human bones.
Another advantage of additive manufacturing is that it allows for distributed production and supply. This can be especially useful in regions where traditional manufacturing facilities are unable to meet demand. Distributed production and manufacturing can also help manufacturers reduce costs by avoiding the need to hold large inventories of goods. This is especially helpful for the pharmaceutical industry, where it can help manufacturers create drugs and vaccines that can be distributed to hard-to-reach places.
A number of industries are utilizing additive manufacturing to streamline their supply chains and improve efficiency. For instance, major aerospace OEMs use AM to make strong, lightweight end-use production parts for aircraft and print tooling quickly and cost-effectively. In addition, medical and dental professionals use AM to fabricate dental models and appliances. Additionally, the energy industry uses additive manufacturing to print parts that improve the manufacture and maintenance of wind turbines.
Material jetting
Material jetting is one of the seven basic additive manufacturing (AM) processes. It works by jetting ultra-thin layers of liquid photopolymer, which is often compared to inkjet printing. The layers are then cured by UV light. This process is very versatile and allows companies to print prototypes in a wide range of materials, colours, textures and rigidity. It also allows for fine surface details and is ideal for producing functional parts.
With this method, you can use a standard digital file and produce prototypes with very accurate dimensions. It also saves you the time and money spent on creating molds. In addition, this method is highly automated and requires little human interaction, which can reduce your overhead costs.
The material jetting process uses thermoset photopolymer resins that are similar to those used in SLA printers. These are cured using UV-light to solidify the printed structure. This technology is capable of printing multiple layers simultaneously and dispensing multiple colours. It can even print complex geometries with varying material properties in different areas of the part. Additionally, it can print supports that are easily removed in the post-processing phase.
This method produces prototypes that are highly detailed and aesthetically pleasing. It is suitable for a number of industries, including aerospace and automotive. It can also be used to create internal voids in a product, which helps make it lighter and more durable. This feature is particularly useful in expensive materials, such as metals.
Material jetting has many benefits, especially for the Design and Engineering departments. Its ability to build complex geometries allows designers to create parts with internal voids and other features, which would be impossible to achieve with subtractive technologies. It also speeds up the production of complex parts, reducing design and assembly times. In addition, it allows engineers to build a single lightweight part with multiple components that could have been produced separately using traditional machining methods. This can significantly improve productivity and increase cost savings. In the long term, this technique will be a significant contributor to future innovation in the manufacturing industry.
3D scanning
3D scanning is an innovative technology that transforms physical objects into dynamic digital representations. This digital representation can then be used as a foundation for modeling and printing, enabling an endless variety of possibilities. It can be used to create complex shapes and parts that cannot be produced using traditional manufacturing methods. 3D scanning can also be used to analyze the as-built condition of an object after it has been manufactured. This is a highly effective way to maintain quality and reduce production costs.
With its wide range of applications, 3D scanning can transform numerous industries. For example, in the construction industry, 3D laser scanning can be used to document existing buildings and structures. This can be done quickly and easily, with minimal disruption to occupants or owners. In addition, it can help avoid expensive rework due to inaccurate data. This enables construction professionals to shorten project schedules and save money by eliminating the need to pay for re-scans.
Moreover, it can be used to inspect the quality of finished products. This is especially important for critical applications such as aerospace, automotive, and medical devices, where quality assurance is crucial. 3D scanning can be used to verify the accuracy of dimensions and surface finish, as well as for identifying flaws and defects. In addition, it can also be used to create accurate virtual models of existing components. This can be useful in analyzing component relationships and optimizing assembly workflows.
One of the most compelling benefits of 3D laser scanning is its ability to provide high-precision measurements in a fraction of the time that manual measurement techniques require. In fact, it can complete tasks that would have taken hours or even days to accomplish by hand in just minutes. This is an incredible advancement in an era where efficiency defines success.
With its wide range of applications, 3D laser scanning can transform numerous industries. For example, it can be used to create complex shapes and parts in the construction industry, and to inspect the quality of finished products in other sectors as well. The possibilities are endless, and with the right tools, you can unlock the full potential of this amazing technology.